A análise de vibração é um método usado na indústria para detectar anomalias em máquinas e motores elétricos.
Através de sensores que transformam a vibração em impulsos elétricos é possível criar relatórios que associam vibrações anormais a possíveis desgastes e anormalidades no dispositivo monitorado.
Temos como exemplo a ABB, uma das maiores fabricantes de motores elétricos do mundo, que possui sistemas de análise de vibração com algoritmos de inteligência artificial que conseguem associar padrões de vibração com suas causas, normalmente desalinhamentos e máquinas operando fora da condição ideal.
A partir da análise de vibração obtemos dados para parâmetros que possibilitam a manutenção preditiva.
As 6 principais causas de falhas em motores elétricos:
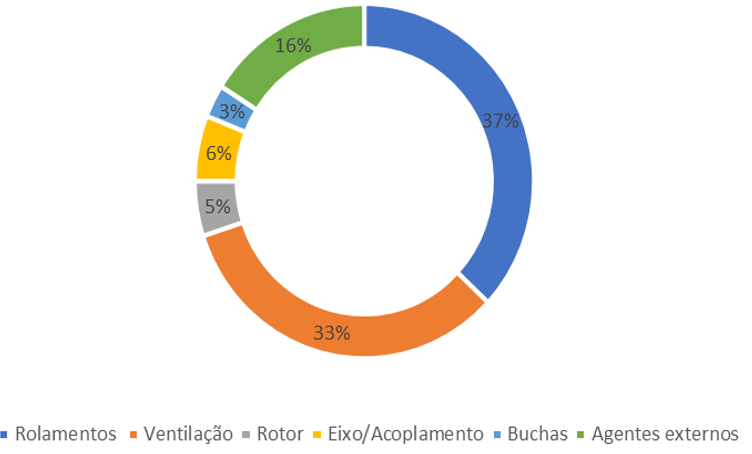
Tipos de problemas de motor 1
As falhas em Rolamentos são a maioria, representando 37% do total. E essas falhas são geradas por:
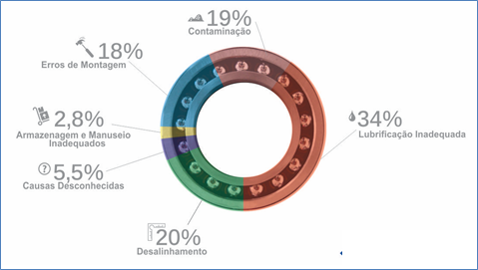
Tipos de problemas de motor 2
E atualmente sabemos o quanto é problemático para uma empresa se um motor elétrico quebra de forma inesperada, causando parada de produção.
É por isso que cada vez mais estudos científicos são feitos atualmente para possibilitar a manutenção preditiva, e muitos deles são relacionados com análise de vibração.
Por que implementar a manutenção preditiva?
Conceituamos a existência de 3 tipos de manutenção (os principais tipos, em nossa visão): a Corretiva, a Preventiva e finalmente, a Preditiva.
- Manutenção Corretiva: correção de falhas em equipamentos que precisam retornar ao funcionamento. Neste caso, a máquina que receberá a manutenção já apresentou falha. Esse tipo de manutenção pode ser:
- Não Planejada: falha inesperada, que interrompe a produção gerando perdas enormes.
- Planejada: queda de rendimento no funcionamento da máquina faz com que técnicos percebam a necessidade de manutenção, planejando-a na próxima parada de produção. Gera perda de produtividade, mas é mais barata que uma manutenção não planejada.
- Manutenção Preventiva: é uma manutenção planejada antecipadamente, que leva em consideração o nível de utilização da máquina e a previsão de sua durabilidade. Gera menos perdas que a Manutenção Corretiva, mas não aumenta a vida útil da máquina.
- E finalmente a Manutenção Preditiva. Por meio do monitoramento da de uma máquina é possível perceber alterações no funcionamento que evidenciem falhas iminentes. E a manutenção preditiva gera economia desta forma: permitindo que se explore todo o ciclo de vida útil de cada máquina e evitando paradas inesperadas.
Portanto percebemos a importância de contar um uma solução inteligente que possibilite a manutenção preditiva.
Como fazer análise de vibração?
Na indústria são usados diversos tipos de sensores para análise de vibração de motores elétricos, mas o princípio físico em geral é parecido: acelerômetros que determinam a intensidade e a frequência da vibração do motor.
- O sensor em primeiro lugar é instalado num ponto estratégico do motor;
- Esse sensor é vinculado a um software que faça a conversão dos dados em informações claras de oscilação;
- Um engenheiro ou técnico experiente em análise de vibração vai correlacionar as informações do software com defeitos característicos do motor monitorado.
Portanto podemos perceber que, em soluções convencionais, é necessário contar com profissionais bem capacitados e softwares complexos para fazer essa implementação.
Porém, podemos fazer de uma forma mais fácil
Porque nós temos um sensor plug and play que fará boa parte do serviço de análise de vibração por você.
Ele é sem fio, por bluetooth, totalmente seguro, e conectado a uma plataforma de virtualização com dados de motores de mais de 130 anos de história da ABB.
Portanto estamos oferecendo mais que um sensor: também entregamos a interpretação dos dados monitorados de análise de vibração.
E é realmente necessário implementar a manutenção preditiva?
Todas as questões relativas à Indústria 4.0 se relacionam com um fator: manter-se competitivo.
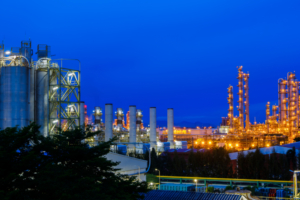
Uma das maiores produtoras de Vodka do mundo, tem apenas uma linha de produção na Suécia para abastecer o mundo inteiro.
Portanto, confiabilidade do processo é essencial para os lucros da companhia.
Ao implementar sensores de vibração (Smart Sensor ABB) a fábrica pôde perceber que tinha rolamentos e bombas próximas de apresentar defeito. Logo após a instalação dos sensores foi possível fazer os reparos necessários em uma parada planejada, evitando assim uma perda substancial de produção.
Imagine o impacto de uma parada de máquinas repentina numa linha que milhões de garrafas por ano. Custo alto, não?
Dê uma olhada agora em nossa solução!
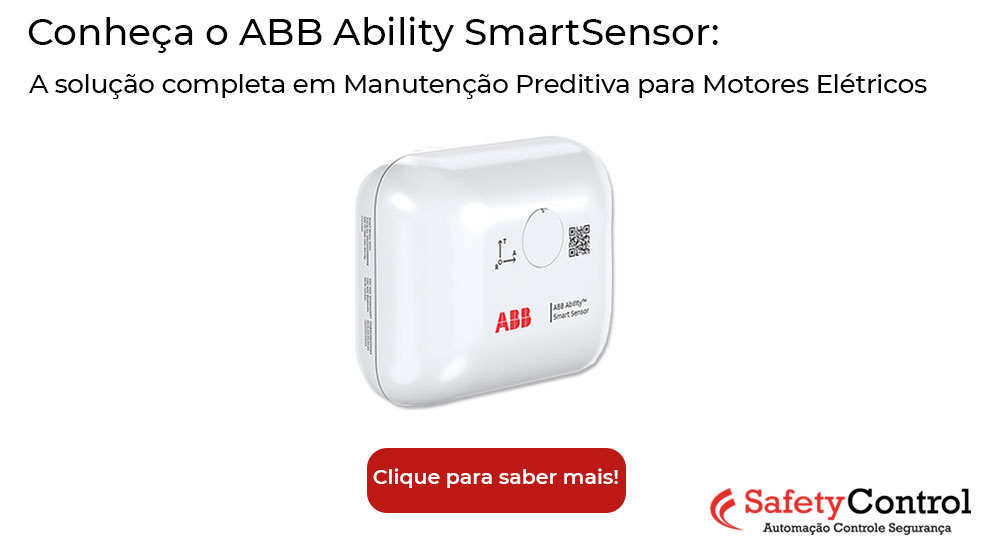
Este conteúdo me ajudou muito, este é um tipo de conteúdo que possui muitas informações importantes.